CONCRETE TIPS
10 Easy Steps To Pouring Your Own Concrete Project
This was written to assist you in planning, completing and enjoying your own do-it-yourself concrete project! By following these steps, you can have a finished concrete project to be proud of!
Step One – Plan Ahead
Laying out your project is an important first step! Stake out your project area. Remove grass, tree roots, etc. Check the grade to ensure proper drainage. Also, be sure to use graph paper and sketch out your project by using the one square equals one foot approach.
Step Two – Forming the Area
The most common forming materials are either 2 x 4’s or 2′ x 6’s. These are placed on the edge to surround the area to be poured. In general, concrete should not be poured at a thickness of less than the width of a 2 x 4. Use stakes on the outside of the form to hold it in place. Note: The stakes must not extend above the form or they will interfere with the “screeding” procedure. Check the grade of the area by moving the “screed” board across the forms and measuring the distance from the board to the grade of the area.
10 Steps to Durable Exterior Flatwork
Exterior concrete flatwork is both beautiful and durable when it is properly placed, finished and protected. In order to ensure that your project is a complete success we strongly suggest you follow these ten steps:
1. Use the right concrete
The Ontario Building Code requires that all exterior concrete shall have a minimum 28-day compressive strength of 32 MPa and a maximum water/cementing materials ratio (W/CM) of 0.45 (C-2 Concrete as per CSA A23.1) and 5-8% air for freeze-thaw durability. 25 MPa concrete should never be used! Concrete should only be ordered from an RMCAO member company.
2. Use the right contractor
Use a contractor who has been trained to an industry certification program such as ACI Concrete Flatwork Finisher/Technician (or similar). Ask for past examples of their work and references. Call the references and visit projects that have gone through at least two winters.
Concrete Driveways
A concrete driveway represents an investment that is designed to last a lifetime, provided proper procedures are followed.
The average homeowner will not normally be able to install a concrete driveway without expert assistance. It is strongly recommended that a qualified contractor be engaged to ensure a satisfactory job.
To provide a quality driveway, the following guidelines should be carefully observed.
(Concrete should be placed between April and September. If placed outside this time frame, additional precautions will be necessary.)
1. Determine The Required Thickness (Minimum)
For cars and pick-ups 100 mm
For light trucks 125 mm
For occasional heavier trucks 150 mm (placed on competent subgrade).
2. Site Preparation
Concrete can be placed directly on uniform subgrade after removing the topsoil, or on deteriorated asphalt pavement. Excavate or bring to grade as necessary using granular ‘A’ as leveling course (typically 100 mm).
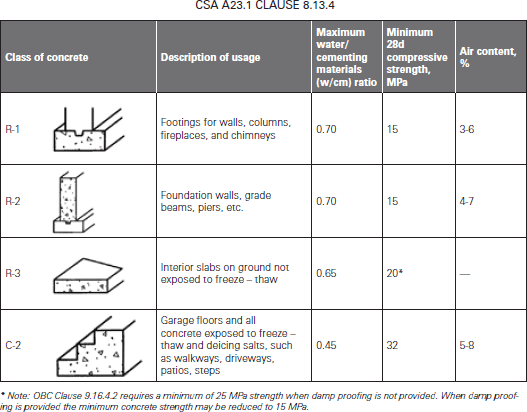
Residential Concrete Requirements
The minimum requirements for residential concrete are outlined in the Ontario Building Code (OBC) and CSA A23.1 – Concrete Materials & Methods of Concrete Construction. In general, the concrete supplied for residential concrete applications shall conform to Table C1 from CSA A438.
Proper Concrete Jointing Details to Control Random Cracking
Shrinkage is an unavoidable fact of concrete construction. The key to a successful concrete project is understanding how to minimize shrinkage and knowing what steps to take to avoid random concrete cracking.
The primary factors that result in concrete shrinkage and/or cracking include:
- Settlement of the sub-grade
- Chemical shrinkage of the concrete
- Temperature and moisture changes in the concrete
- Application of loads to the concrete surface
- Restraint of concrete movement during either expansion or contraction.
The actual amount of concrete shrinkage is governed by:
The concrete’s raw constituents
The unit water content of the mix
The drying conditions that the concrete is exposed to
The size and shape of the concrete element.
Sealers for Concrete Flatwork
Exposed concrete surfaces can benefit significantly from the application of concrete sealers to repel the infiltration of water, chlorides and provides short term protection from chemical spills and stains.
In general, there are two types of sealers available for use:
- Film Forming Sealers – Sealers that bond to the top surface of the concrete provide a barrier to the ingress of liquids.
- Penetrating Sealers – Sealers that are absorbed into the concrete surface and block the pore structure of the concrete preventing further water penetration.
Selection of the proper concrete sealer is based upon understanding the required concrete surface finish and the exposure conditions and traffic type (vehicles, pedestrian, etc.) that the sealer will be exposed to. It is strongly recommended that you discuss your application with the sealer manufacture prior to the start of the project. The factors that should be considered include:
What Every Homeowner Should Know About Concrete
What is concrete?
In its simplest form, concrete is a mixture of paste (cement & water) and aggregates (sand & stone). The paste coats the surface of the fine (sand) and coarse (stone) aggregates and binds them together into a rocklike mass known as concrete. In addition to paste and aggregates, concrete may also contain highly specialized chemical admixtures that enhance the specific properties of concrete. Chemical admixtures are used to improve both the workability and/or the durability of concrete.
Within this process lies the key to a remarkable trait of concrete: it is plastic and can be molded or formed into any shape when newly mixed, and is strong and durable when hardened. These qualities explain why concrete is a primary building material throughout the world that is used to construct everything from skyscrapers, bridges, highways and dams to sidewalks, curbs, patios and houses.
Hot Weather Concrete
Weather conditions can have a dramatic effect on both the setting time and concrete placing, finishing and protection systems that must be followed for proper concrete placement.
Hot weather concreting conditions typically include:
- High ambient air temperatures (? 28°C)
- Low relative humidity conditions
- High wind speeds
- Solar radiation or heat gain
These conditions can result in the following challenges for the concrete contractor:
- Increased concrete water demand
- Accelerated concrete slump loss
- Increased rate of setting leading to placing and finishing difficulties
- Increased tendency for plastic shrinkage cracking
- Increased concrete temperature resulting in lower ultimate strength
- Increased potential for thermal cracking
Cold Weather Concreting
Weather conditions can have a dramatic effect on both the setting time and concrete placing, finishing and protection systems that must be followed for proper concrete placement. Cold weather concreting conditions are typically defined as:
- When the air temperature is ? 5°C.
- Or when there is a probability that the temperature may fall below 5°C within 24 hours of placing the concrete.
Because the hydration process is a chemical reaction it is strongly affected by ambient air and subgrade/formwork temperatures. At low temperatures concrete gains strength and sets very slowly and must be adequately protected from freezing and thawing. Concrete that is allowed to freeze while in its plastic state can have its potential strength reduced by more than 50% and its durability properties will be dramatically reduced. Concrete must achieve at least 3.5 MPa before it is frozen and should obtain at least 20 MPa before it is exposed to multiple freeze/thaw cycles.